At Cyntek, we provide top-quality engineering consulting services to businesses and organizations in a variety of industries. Our team of experienced engineers has expertise in a range of fields. We offer a wide range of services, including Front-end engineering design and Continuous improvement. Our goal is to help our clients achieve their objectives and stay ahead of the competition.
Service:
Consulting Services
Front-End Engineering Design
No matter the industry or application, Cyntek believes that a thorough front-end engineering design (FEED) process is an essential step in any capital project.
Project initiation can be driven by a wide array of internal and external factors including, but not limited to, strategic, financial, social, environmental, and regulatory considerations. Typically, there are two scenarios where front-end engineering design is applied:
- Planning for a project that is mandated by enterprise environmental factors
- Evaluating the return-on-investment for proposed projects
In certain scenarios, projects are initiated based on a regulatory requirement, or due to a mandate given by Senior management. When a project is mandated by enterprise environmental factors, the use of front-end design ensures that the project scope is defined, and project risks are identified at the onset of the project in an effort to mitigate the likelihood of schedule and cost overruns during implementation.
For projects that produce a desirable (rather than mandatory) outcome, the use of a FEED process provides the same benefits as those described above, with the added benefit of introducing “go/no-go” decision gates. The inclusion of decision gates allows our clients to evaluate whether the project can be justified as the level of project definition increases.
The first step in performing the FEED process is to conduct a project walkthrough to gather high-level requirements. By generating an understanding of the project requirements and comparing them to the current state, Cyntek’s project managers can make a determination on the level of front-end engineering applied to a given project. Each FEED process is tailored to our clients based on the project initiation drivers and their unique priorities. In all front-end engineering design engagements, Cyntek utilizes a proprietary industrial cost engineering tool to analyze the financial implications of various design decisions.
A typical front-end engineering design process utilized by the Cyntek team for packaging automation projects is summarized in the following graphic.
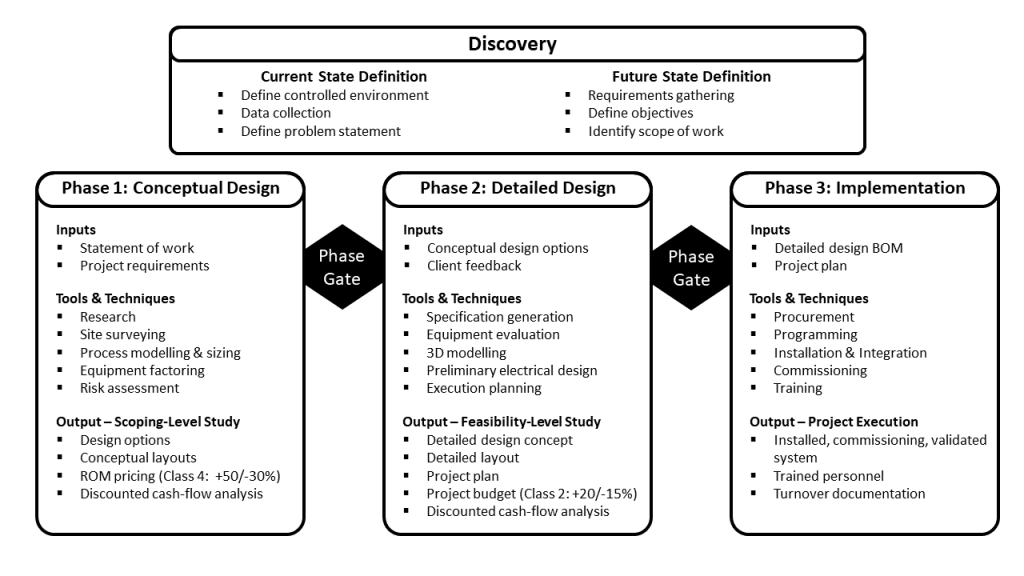
Continuous Improvement
Continuous improvement is the ongoing improvement of products, services, or processes through incremental changes. Continuous improvement is a hallmark of the Toyota Production System (TPS), often referred to as “lean manufacturing” which is a manufacturing philosophy that aims to eliminate waste and achieve the best possible efficiency.
Many process frameworks have been devised to guide continuous improvement initiatives such as the Plan, Do, Check, Act (PDAC) cycle and the Define, Measure, Analyze, Improve, Control (DMAIC) process. These processes can be implemented as a standalone quality improvement procedure but are often part of a larger process improvement initiative such as Sig Sigma, or Lean.
The Cyntek team has experience conducting continuous improvement initiatives in a diverse set of industries and applications. At Cyntek we have devised our own process for completing continuous improvement initiatives that is a variation of the DMAIC process. An example process used to conduct a continuous improvement initiative in a manufacturing environment is outlined below:
- Problem Recognition
- Requirements gathering (performance, operational, life cycle, compliance/quality, etc.)
- Recognition that processing problems exist (i.e. defect rate, throughput, maintenance frequency, downtime, etc.) by benchmarking KPIs with performance requirements. This is typically completed by our clients and is the driver for the initialization of a continuous improvement initiative, however, our team can use different tools at our disposal to aid in the problem recognition phase.
- Avoid defining the cause of the problem – simply identify that one exists
- Tools: Stakeholder Interviews, Value Stream Mapping (VSM), Incidence Matrix
- Baseline Manufacturing Process Analysis
- Define (Process)
- Process definition (record process flow, define steps, record equipment index, record operator index)
- Determine all production resources (i.e. equipment, operators, materials, methods, environment) and resource attributes (activity, quantity, position, function/type, performance)
- Tools: PFD, Process VSM, Swimlane Diagram
- Measure
- Data collection (quantitative analysis) and observations (qualitative analysis)
- Analyze
- Creation of a process model to calculate Takt time, line of balance rate, and motion analysis
- Classify activities as value-added (VA), necessary but non-value added (NNVA) and non-value added (NVA)
- Identify process waste (i.e. motion, inventory, waiting, defects, overproduction, transportation, and overprocessing)
- Tools: Pareto Chart, Root-cause Analysis, Failure Mode and Effects Analysis (FMEA), Fishbone Diagram
- Define (Process)
- Problem Definition
- Using the Baseline Manufacturing Process Analysis, identify the root cause of the processing problem, and define the problem statement.
- Define the controlled project environment (inputs/outputs)
- Define the scope of the process improvement and estimate the design work required to develop a solution to the problem statement
- Suggest high-level improvement actions to estimate the cost (+50% to -20%) of implementing a solution to the problem statement
- Phase Gate – Do the proposed benefits of the solution outweigh the estimated costs associated with a solution (design fees, hardware, etc.)?
- Design Modifications
- The design process is highly variable depending on the nature of the process problem. Typically, the design process will encompass research, specification building, and risk assessments, and may include the use of six sigma tools such as design of experiments (DOE) and prototyping.
- Evaluate & Propose
- Submit request for proposals/quotes based on a user requirements specification (URS)
- Evaluate design options against the URS
- If necessary, build prototype, follow DOE, or conduct vendor tests
- Define the scope of work required to implement a solution
- Create proposal for solution implementation including costs, schedule, and discounted cash flow analysis
- Phase Gate – Does the proposed solution meet the future state requirements?
- Implement & Control
- Following proposal acceptance, the execution of the project will commence.
- Emphasis is placed on controlling the process to generate feedback on the efficacy of the solution and determine whether any revisions are necessary.